FALLSTUDIE
Automatyczny rozładunek i opasanie elementów z linii rozkroju

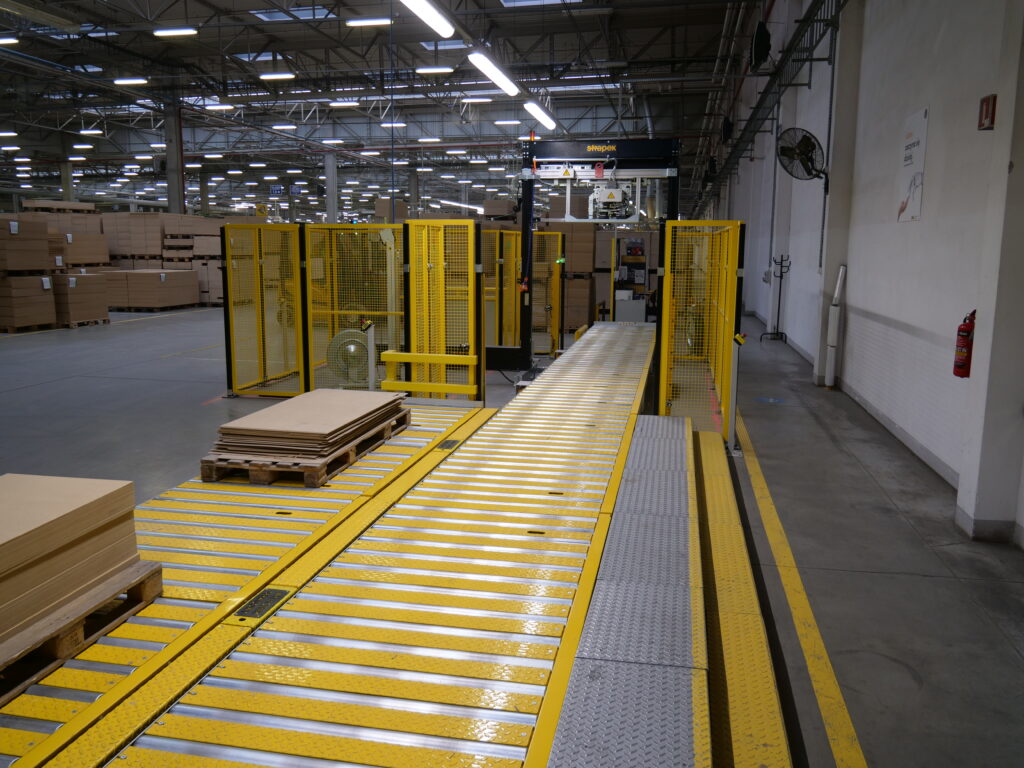
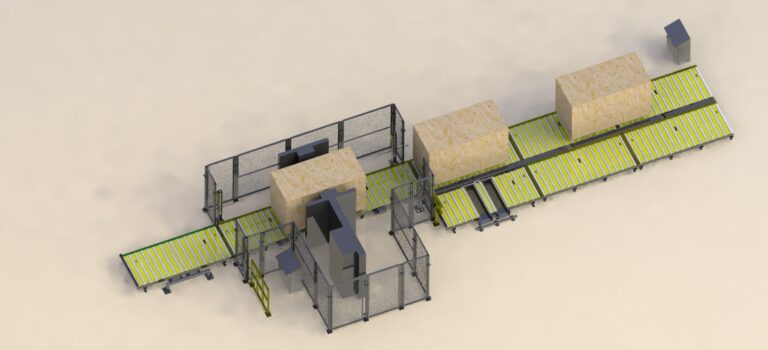
Postawiliśmy sobie za zadanie stworzenie projektu, który pozwoli na zautomatyzowanie procesu transportu gotowych detali z linii rozkroju i mechaniczne opasanie. Dysponujemy linią, która umożliwia automatyczne opasanie poukładanych na podkładzie lub palecie płyt wiórowych o określonych parametrach.
Opis działania układu
w czasie transportu samochodowego.
Unser Projekt zielt darauf ab, den Transport vorgefertigter Teile von der Schneidlinie bis zur mechanischen Umreifung zu automatisieren. Unsere Anlage ermöglicht die automatische Umreifung von Spanplatten mit spezifischen Parametern, die auf Unterlagen oder Paletten platziert werden.
Systembetrieb
Abmessungen der Trägerplatten: 20 mm × 800 mm × 2000 mm
Palettenabmessungen: 150 mm × 800 mm × 2000 mm
Beladung der transportierten Bretter:
– stapelbreite max. 1100 mm
– stapellengte max. 2500 mm
– stapellänge max. 1500 mm
Formierka kartonów typ FK-01

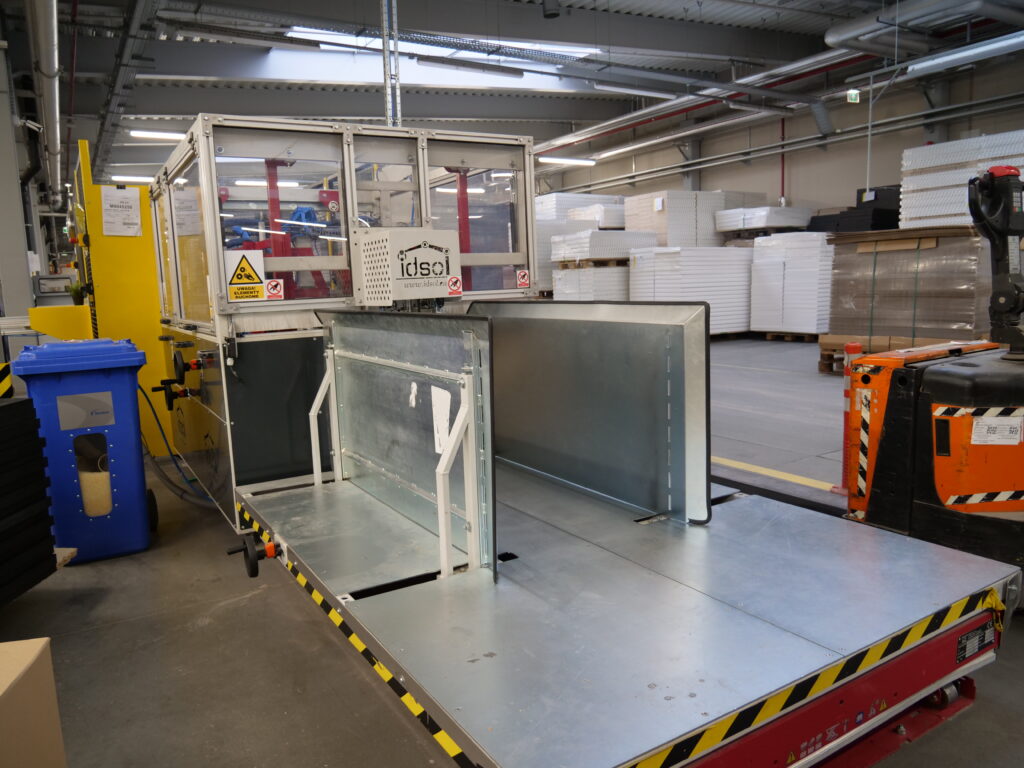
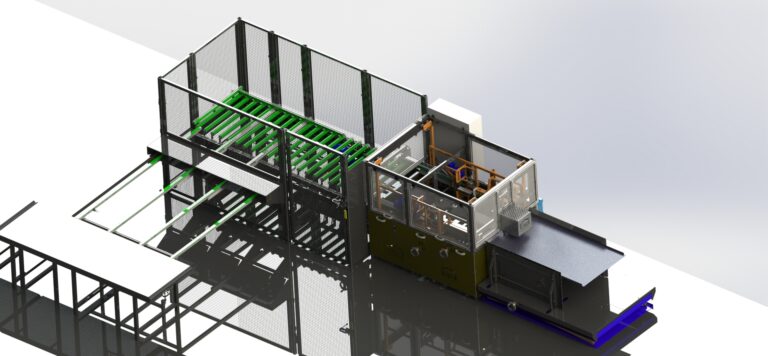
Formierka kartonów powstała w celu zautomatyzowania procesu klejenia kartonów, który wcześniej był wykonywany manualnie. Do wykonania zadania były oddelegowane cztery osoby, a jakość uformowanego kartonu pozostawiała wiele do życzenia, ponieważ był on składany za pomocą specjalnych zamków, a nie klejony. Dlatego też postanowiliśmy zaprojektować i stworzyć maszynę, która pozwoli na perfekcyjne formowanie i klejenie nawet dwunastu sztuk kartonów w ciągu zaledwie jednej minuty. Załadunek formatek kartonów na podnośnik nożycowy odbywa się co prawda ręcznie, jednak cały proces formowania, klejenia oraz podania kartonu w linie przebiega już w trybie automatycznym. Przy klejeniu wykorzystujemy klej termokurczliwy.
Die Kartonformmaschine wurde entwickelt, um den bisher manuell durchgeführten Prozess des Kartonklebens zu automatisieren. Zuvor waren vier Personen für diese Aufgabe zuständig, was zu einer unzureichenden Qualität der geformten Kartons führte, da sie mit Spezialschlössern und nicht mit Klebstoff zusammengebaut wurden. Aus diesem Grund haben wir beschlossen, eine Maschine zu konstruieren und zu bauen, die das präzise Formen und Kleben von bis zu zwölf Kartonstücken in nur einer Minute ermöglicht. Das Beladen der Kartonformen auf die Scherenhebebühne erfolgt manuell, jedoch erfolgt der gesamte Prozess des Formens, Klebens und Zuführens der Kartons in die Linien automatisch. Für das Kleben verwenden wir Heißkleber.
Abmessungen der Box
Minimal:
Breite – 400 mm
Länge – 1000 mm
Höhe – 3 mm
Maximal:
Breite – 800 mm
Länge – 2000 mm
Höhe – 5 mm
Effizienz von 12 Stück/60 Sek
Wir bieten auch die Möglichkeit, eine personalisierte Maschine entsprechend den individuellen Bedürfnissen des Kunden herzustellen.
Magazyn buforowy między maszynami obróbczymi a lakiernią

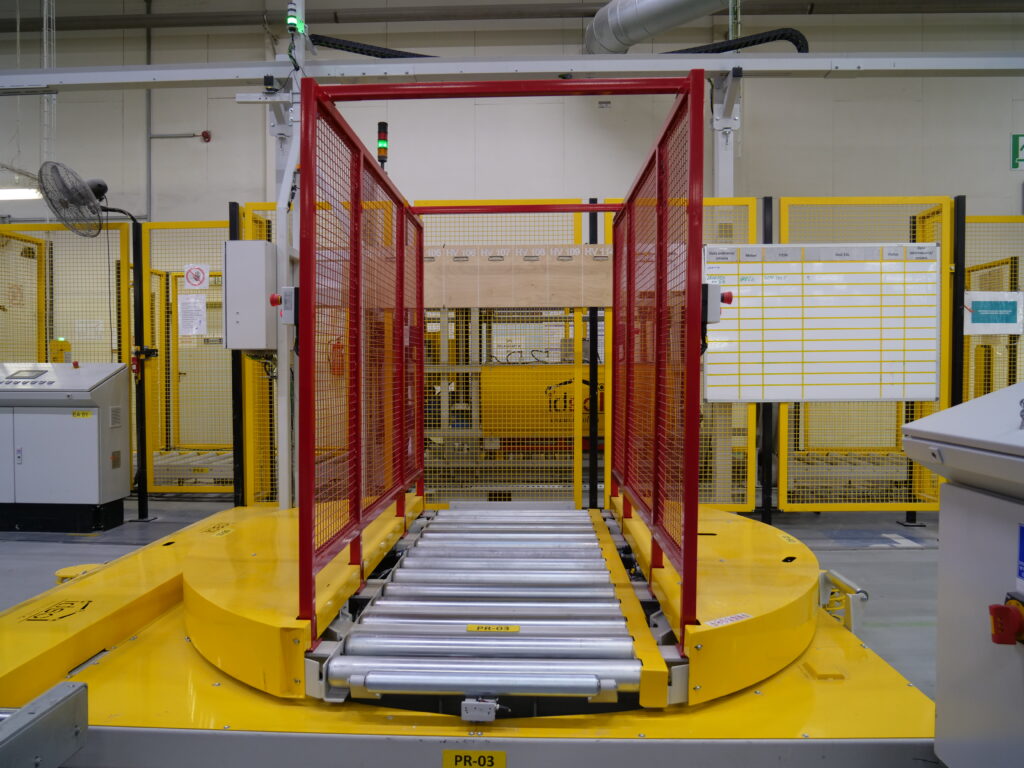
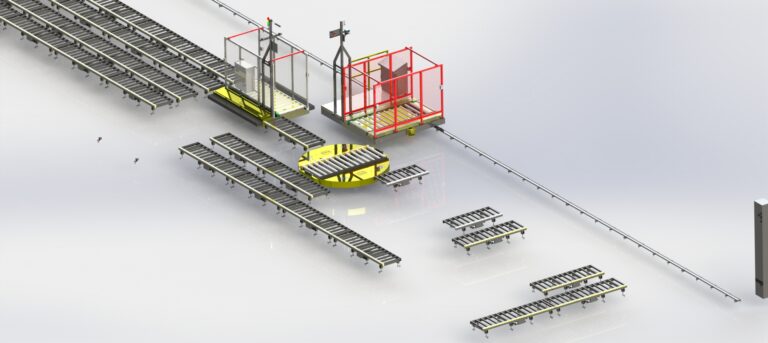
Magazyn buforowy został zaprojektowany w celu usprawnienia transportu międzyoperacyjnego, który wcześniej był realizowany za pośrednictwem urządzeń obsługiwanych ręcznie. Pracownicy zmuszeni byli manualnie przesuwać paczki po transportach rolkowych nienapędzanych. Podobnie wyglądała sytuacja w przypadku transportu poprzecznego i obrotu. Taki proces nie tylko był pracochłonny i niezbyt wydajny, ale wymagał też zaangażowania ogromnej liczby pracowników i nierzadko obfitował w uszkodzenia transportowanych detali. Opracowana automatyzacja pozwoliła raz na zawsze pożegnać się ze wszystkimi wymienionymi problemami. Linia umożliwia bowiem automatyczne magazynowanie gotowych do malowania elementów po obróbce i ich transport do kolejnego procesu produkcyjnego.
Automatyzacja linii polega na odbiorze przez zasilaną indukcyjnie przesuwnicę ułożonych w stos na podkładach półfabrykatów meblowych z linii obróbczej. W zależności od zapotrzebowania elementy będą transportowane na obszar napraw za pośrednictwem przenośników rolkowych lub bezpośrednio na obrotnicę, a następnie dalej przez przenośnik rolkowy na przesuwnicę rozdzielającą gotowe elementy pomiędzy buforami rolkowymi.
Gotowe pakiety półfabrykatów meblowych są pobierane z buforu za pomocą przesuwnicy z obrotnicą i transportowane na linię lakierniczą. Przesuwnica zasilana indukcyjnie posiada możliwość bezpośredniego podawania elementów na przesuwnicę z obrotnicą.
Das Pufferlager wurde konzipiert, um den betriebsübergreifenden Transport zu verbessern, der bisher manuell mit nicht angetriebenen Rollentransporten durchgeführt wurde. Mitarbeiter mussten Pakete manuell bewegen, was nicht nur arbeitsintensiv und ineffizient war, sondern oft auch zu Schäden an den transportierten Teilen führte. Durch die Automatisierung konnten wir diese Herausforderungen erfolgreich überwinden. Unsere Linie ermöglicht nun die automatische Lagerung lackierfertiger Elemente nach der Bearbeitung und deren reibungslosen Transport zum nächsten Produktionsschritt.
Die Automatisierungslinie übernimmt Möbelhalbzeuge von der Verarbeitungslinie auf Schwellen und nutzt einen induktionsbetriebenen Förderer. Je nach Bedarf werden die Elemente entweder direkt zum Reparaturbereich oder über Rollenbahnen zum Drehtisch transportiert. Anschließend werden sie über Rollenbahnen zum Verschieber weitergeleitet, der die fertigen Elemente auf Rollenpuffer verteilt.
Fertige Pakete mit Möbelhalbzeugen werden dann über ein Förderband mit Drehteller aus dem Puffer entnommen und zur Lackierstraße transportiert. Der induktionsbetriebene Schlitten ermöglicht es, Elemente mit einem Drehteller direkt auf den Schlitten zu übergeben.
Abmessungen der Trägerplatte: 1200 × 600 × 20, 2000 × 600 × 20
Anordnung der Elemente auf der Trägerplatte:
Elemente gestapelt mit einem Gesamtgewicht von 1000 kg
Abmessungen einzelner Elemente:
– Länge: 300-2200 mm
– Breite: 44-1000 mm
– Dicke: 6-30 mm
Maximales Ladegewicht: 2000 kg
Transporthöhe: 300 mm
Transportgeschwindigkeit: 15-20 m/min
Pufferung: bis zu 100 Pakete
Magazyn rolkowy akumulacyjny elementów meblowych

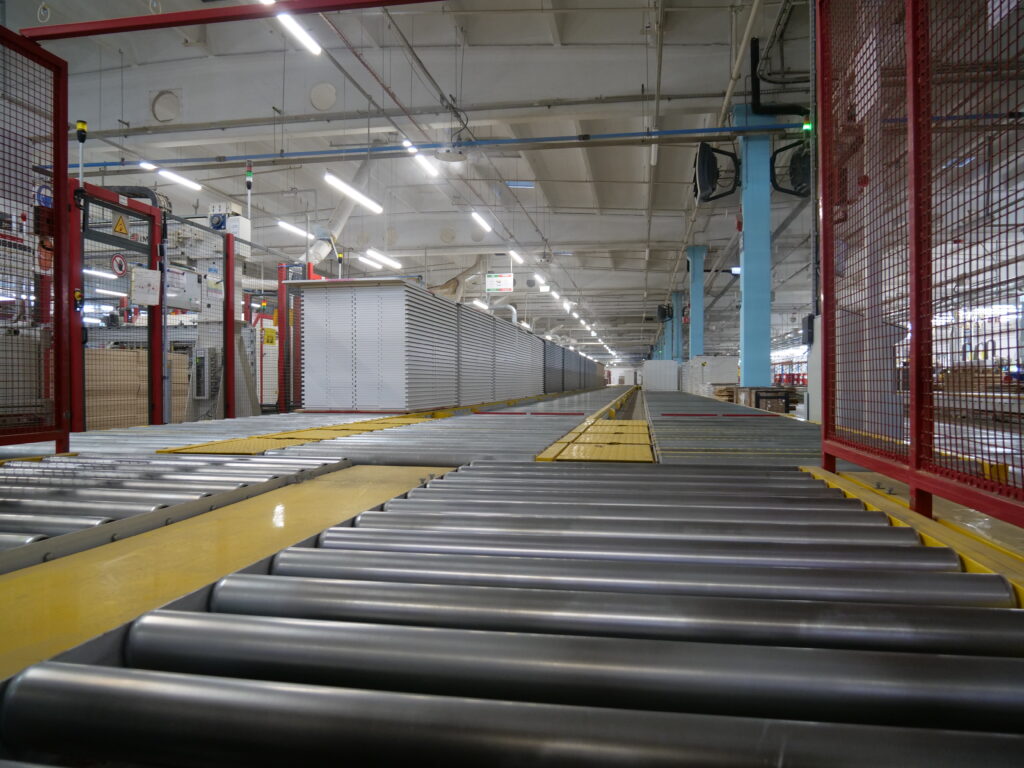
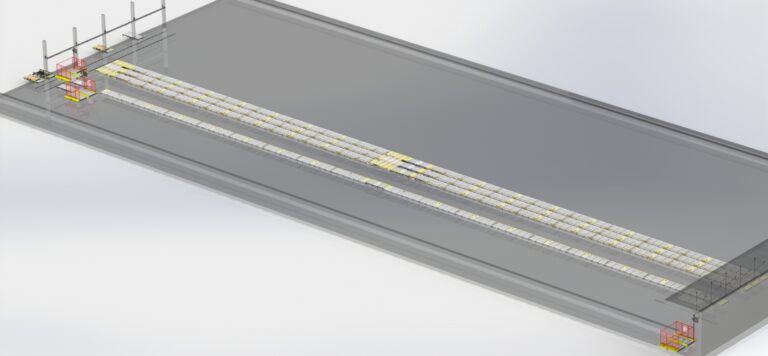
Proces magazynowania wcześniej był realizowany poprzez stawianie pakietów produktów na posadzce hali. Skutkowało to dużym ruchem wózków widłowych w obszarze poruszania się pracowników, co z kolei przyczyniało się do częstych uszkodzeń transportowanych elementów. Transport międzyoperacyjny wymagał też zaangażowania przynajmniej kilku pracowników.
Automatyczny magazyn pozwala na ogromne usprawnienie całego procesu i eliminację niedogodności, z którymi musieliśmy się dotąd mierzyć. Dzięki wykorzystaniu rolek akumulacyjnych automatyczna linia w pełni wykorzystuje potencjał magazynowy zaprojektowanej linii.
Bisher wurden Möbelelemente durch Stapeln von Produktbündeln auf dem Hallenboden gelagert. Dies führte zu einem hohen Verkehrsaufkommen von Gabelstaplern im Bereich der Durchgangswege der Mitarbeiter, was wiederum häufig zu Schäden an den transportierten Elementen führte. Auch der zwischenbetriebliche Transport erforderte die Beteiligung von mindestens mehreren Mitarbeitern.
Ein automatisches Lager ermöglicht eine erhebliche Verbesserung des gesamten Prozesses und die Beseitigung der bisherigen Unannehmlichkeiten, mit denen wir konfrontiert waren. Durch den Einsatz von akkumulierenden Rollen nutzt die automatische Linie das volle Lagerpotenzial der konzipierten Linie optimal aus.
Der Empfang von Paketen erfolgt über eine zweiständige Rollenrutsche, die als Beladung für das Lager dient. Beim Beladen greift die Rutsche die Informationen von der Abnahmelinie ab, um die Art der transportierten Ladung zu identifizieren, und leitet sie dann an die Rollenförderer des Lagers weiter. Das Lagersteuerungssystem ermöglicht es dem Bediener, die Standorte der Palettentypen auf den verschiedenen Linien zu überwachen. Zusätzlich bietet das System einen aktuellen Überblick über die Anzahl der Paletten nach Typen aufgeteilt. In drei Rollenförderlinien wurden zwei Stationen mit dreifachen Hubtischen installiert (eine in der Mitte und eine am Ende der Linie), um eine effizientere Steuerung des Paketverkehrs auf den Rollenbahnen zu ermöglichen.
Die Entnahme von Paletten aus dem Lager erfolgt ebenfalls über eine zweiständige Rollenrutsche, die auch für das Beladen von Paketen in die Produktionslinien zuständig ist. Es besteht die Möglichkeit, Produkte auf Paletten zu liefern, wobei das maximale Ladegewicht 1500 kg beträgt.
Obrotnica pionowa pakietów OB.-01

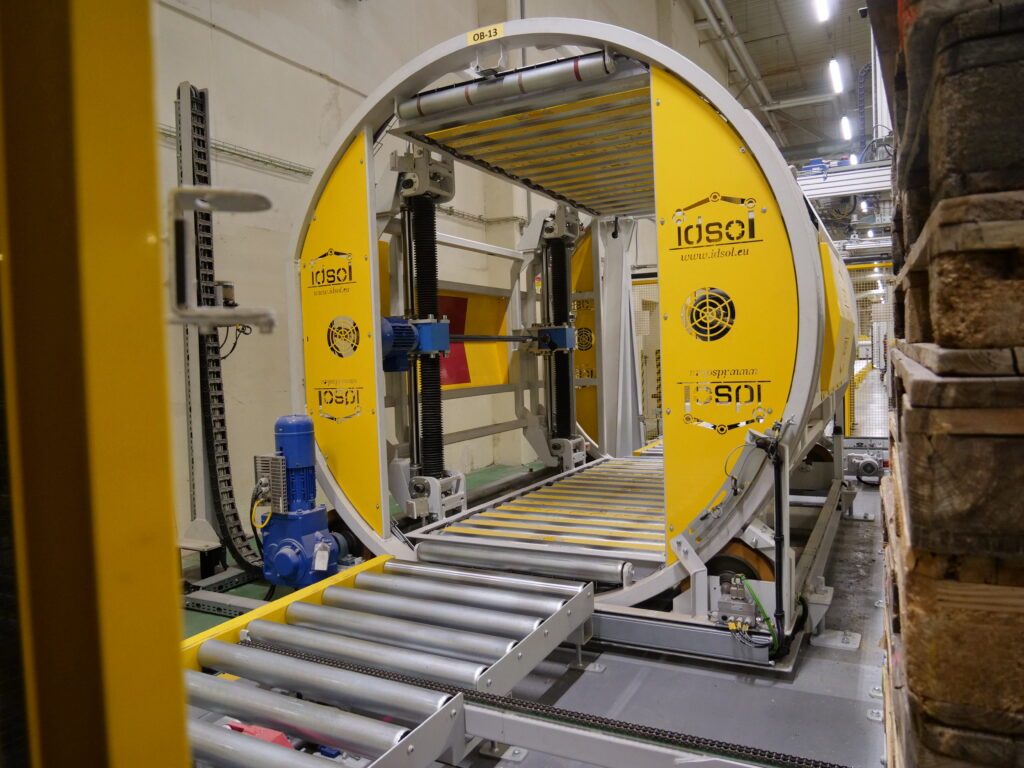
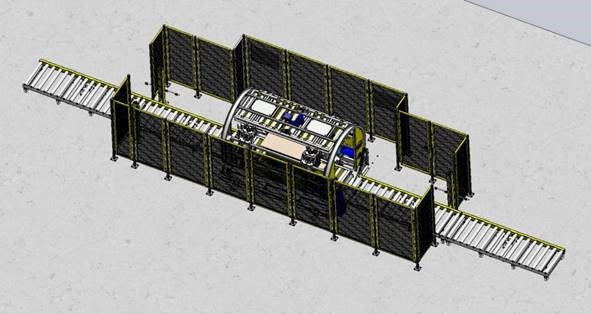
Obrotnica pionowa pakietów to urządzenie, którego podstawowym i zarazem wyróżniającym wariantem pracy jest funkcja obrotu pakietów o 180° w osi pionowej. W standardzie mamy również mechanizm stabilizacji bocznej, który zabezpiecza przed niekontrolowanym rozsunięciem się ze sztaplowanego ładunku podczas obrotu sztapla. W zależności od wymaganej wydajności i wysokości pakietu wykonujemy urządzenia, w których ściskamy obracany towar jedną lub dwiema półkami z nabudowaną nawierzchnią rolkową.
Wariantowo wykonujemy także:
— trzymania podkładów za pomocą ssawek, wykorzystując podciśnienie generowane przez eżektor,
— trzymanie palet,
— bez w/w funkcji,
— układy hybrydowe, gdzie materiał wjeżdża na podkładzie, a przed wjazdem w obrotnicę kładziemy paletę za pomocą manipulatora.
Der vertikale Paketdrehtisch ist eine Vorrichtung, die Pakete standardmäßig um 180° um die vertikale Achse dreht. Zusätzlich verfügt er über einen seitlichen Stabilisierungsmechanismus, der ein unkontrolliertes Verrutschen der gestapelten Ladung während der Drehung verhindert. Je nach benötigter Effizienz und Höhe der Verpackung bieten wir Geräte an, die die gedrehten Pakete mit ein oder zwei Regalen mit eingebauten Rollenoberflächen komprimieren.
Alternativ bieten wir auch:
– Halterungen für Pakete mit Saugnäpfen, die das Vakuum des Ejektors nutzen,
– Halterungen für Paletten,
– Systeme ohne die oben genannten Funktionen,
– Hybridlösungen, bei denen das Material auf einer Plattform zugeführt wird und wir die Palette vor dem Eintritt in den Drehtisch mithilfe eines Manipulators platzieren.
Das Sortiment an gedrehten Paketen umfasst drei Größenvarianten:
-
Klein:
– Maximale Stapelgröße rotierender Elemente: Länge 2500 mm × Breite 900 mm × Höhe 1400 mm
– Minimale Stapelhöhe rotierender Elemente: 800 mm
– Mindestbreite des gedrehten Stapels: 300 mm
– Max. Gewicht eines Stapels rotierender Elemente: 1500 kg
- Mittelgroß:
– Maximale Stapelgröße rotierender Elemente: Länge 2500 mm × Breite 1300 mm × Höhe 1500 mm
– Minimale Stapelhöhe rotierender Elemente: 900 mm
– Mindestbreite des Drehstapels mit Seitenstützfunktion: 600 mm
– Max. Gewicht eines Stapels rotierender Elemente: 2250 kg
- Groß und schwer (z. B. HDF-Platten):
– Maximale Stapelgröße rotierender Elemente::
– Länge 2400 mm × Breite 800 mm × Höhe 1300 mm, Elementgewicht ~ 2500 kg
– Länge 2000 mm × Breite 1250 mm × Höhe 1300 mm, Elementgewicht ~ 3000 kg
– Minimale Stapelhöhe rotierender Elemente: 800 mm
– Mindestbreite des Drehstapels mit Seitenstützfunktion: 400 mm
– Max. Gewicht eines Stapels rotierender Elemente: 3000 kg
Die Taktzeit des Drehtellers selbst (mit Ein- und Auslauf von Stapeln mit einer Mindesthöhe von 900 mm) beträgt ca. 120 Sekunden.
Die Zykluszeit hängt im Allgemeinen von der Höhe und Breite des gedrehten Stapels ab und variiert zwischen 60 und 90 Sekunden.
Der Zugang von Personen zum Arbeitsbereich der Wendestation wird durch eine Zaunanlage mit optischem Sicherheitssystem verhindert. Das Gerät ist mit einem zentralen Schmiersystem ausgestattet, das den ordnungsgemäßen Betrieb des Kompressionsmechanismus gewährleistet. Zusätzlich verfügen die Spannschrauben über Ziehharmonika-Abdeckungen zum Schutz vor Schmutz durch die gedrehten Stapel.
Przenośniki służące do obsługi poziomów pracy technologicznej

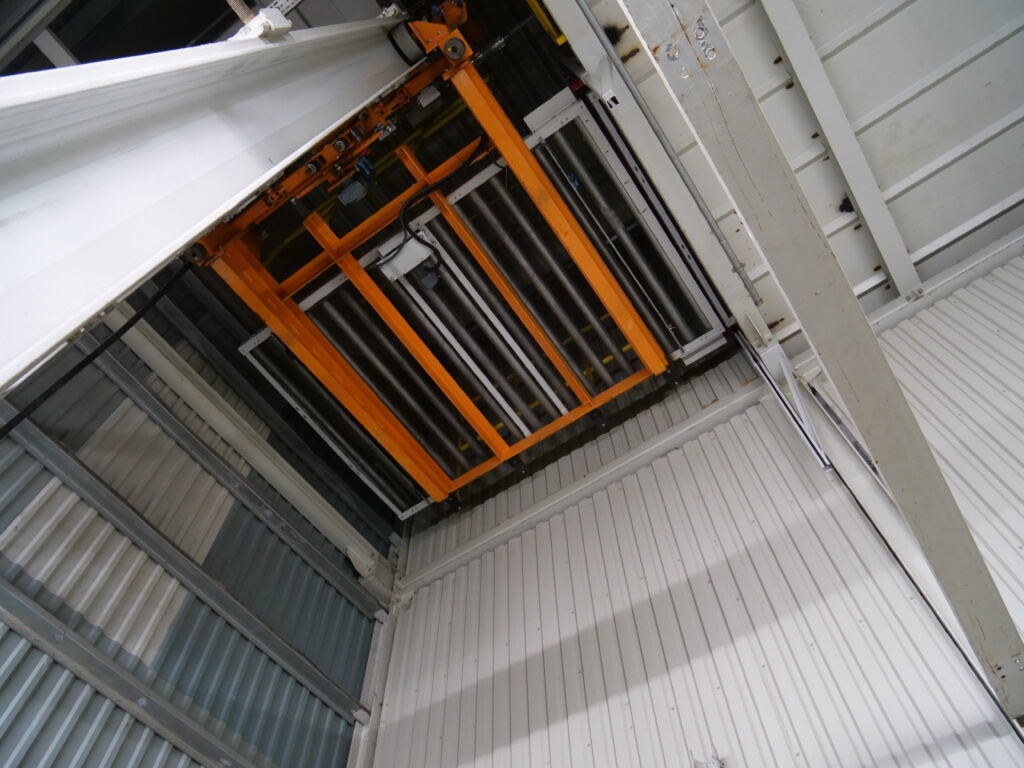
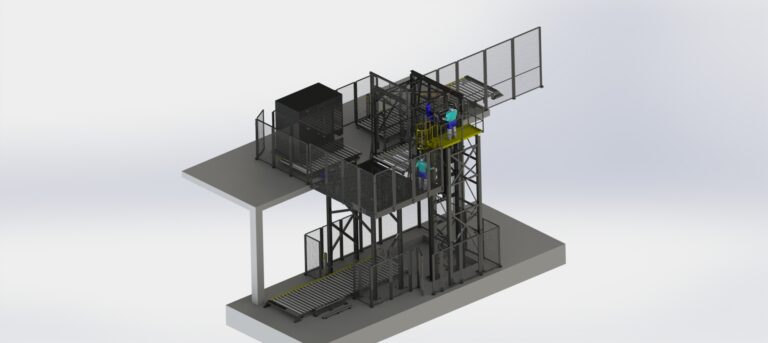
Przenośniki pionowe to urządzenia, które umożliwiają automatyczny transport między różnymi poziomami gotowych półfabrykatów meblowych do magazynu znajdującego się na antresoli na wysokości 6 m. Sekcja unoszenia pracuje bezobsługowo w strefie wygrodzonej, oznakowanej i zabezpieczonej przed wtargnięciem osób niepożądanych.
Vertikalförderer sind Geräte, die den automatischen Transport fertiger Möbelhalbzeuge zwischen verschiedenen Ebenen bis zu einem Lager im Zwischengeschoss in einer Höhe von 6 m ermöglichen. Der Hubmechanismus arbeitet in einem umzäunten, markierten Bereich, der vor dem unerlaubten Zugang geschützt ist.
Abmessungen der unterstützten Paletten:
- Abmessungen der EURO-Palette: Breite × Länge = 800 × 1200 mm
- Abmessungen der EURO-Großpalette: Breite × Länge = 800 × 2000 mm
- Ladungsabmessungen: Breite × Länge × Höhe = 2000 × 2600 × 2500 mm
- Beladungsgewicht: max. 2000 kg
- Transportgeschwindigkeit: 15-40 m/min
- Systemeffizienz: von 30 bis 100 Pakete/h
Beschreibung des Systembetriebs
Die Last gelangt auf Rolltische und dann auf einen vertikalen Transportförderer, der sie auf eine höhere Ebene transportiert. Die Palette wird auf einen Rollenförderer übergeben, der die fertigen Halbzeuge auf Rolltische transportiert, die direkt mit dem Lager im Zwischengeschoss verbunden sind.
Durch den Einsatz des automatischen Vertikaltransports konnten wir die Effizienz des gesamten Lagers deutlich verbessern und eine erhebliche Anzahl von Mitarbeitern entlasten, die für die Koordinierung der Transportvorgänge erforderlich sind.
Durch den Einsatz einer zusätzlichen Stoßstange vor und neben der Rollenbahn ist es möglich, fertige Pakete mit Gabelstaplern direkt an die Förderanlage zu liefern.
Robotyzacja podawania i odbioru elementów do wiertarki

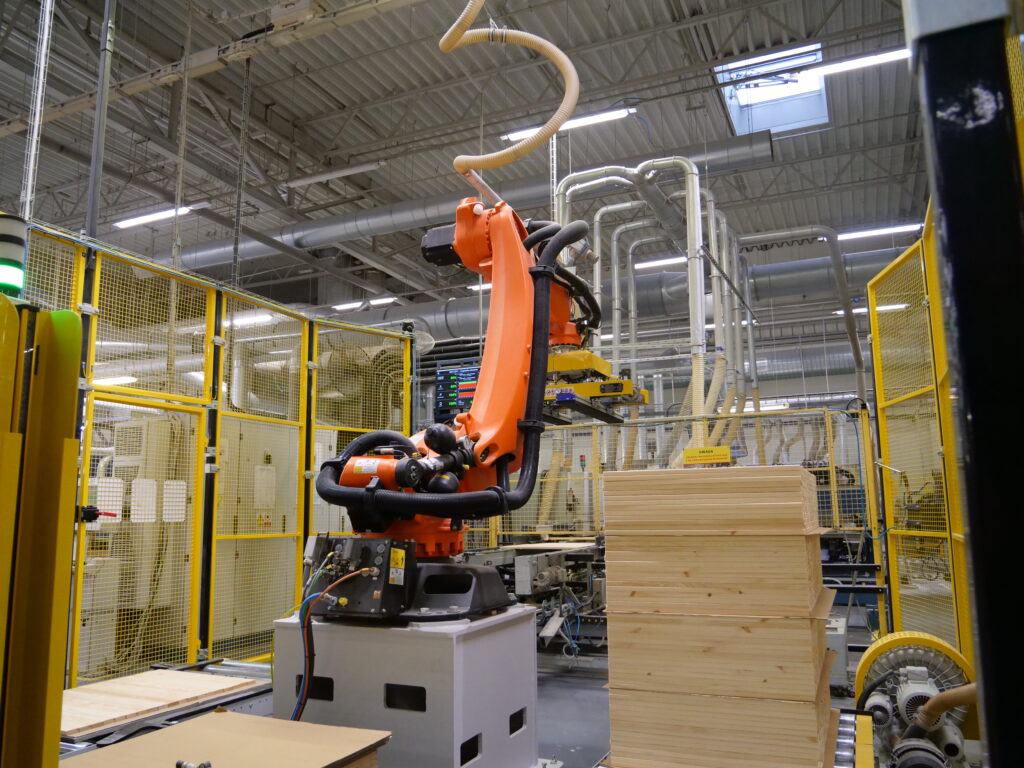
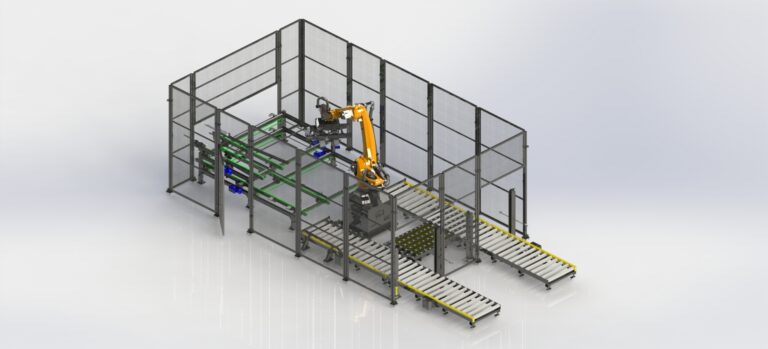
Proces załadunku i odbioru elementów był wcześniej realizowany przez operatora maszyny, a wydajność oscylowała na poziomie 10-12 szt./min. Brak powtarzalności ułożenia elementów po operacji wiercenia generował problemy w dalszym przebiegu produkcji. Robotyzacja układu pozwoliła na poprawę wydajności do 20 szt./min. Uzyskaliśmy dzięki temu pożądaną powtarzalność ułożeń i stałą wydajność całego układu, a także zmniejszyliśmy liczbę osób potrzebną do obsługi urządzeń
Bisher wurde das Laden und Entladen der Werkstücke manuell durch den Maschinenbediener durchgeführt, was zu einer Effizienz von etwa 10–12 Stück pro Minute führte. Aufgrund der unzureichenden Genauigkeit bei der Platzierung der Werkstücke nach dem Bohren traten Probleme im weiteren Produktionsprozess auf. Durch die Einführung von Robotertechnik wurde die Produktivität auf 20 Stück pro Minute gesteigert. Dies ermöglichte eine präzisere Platzierung der Werkstücke und eine konstant hohe Effizienz des gesamten Systems. Gleichzeitig konnte die Anzahl der Bediener, die zur Steuerung der Geräte benötigt werden, reduziert werden.
Ein Elementstapel wird über eine Rollenbahn in die Roboterzelle eingeführt. Dort nimmt ein Roboter mit Vakuumgreifer zwei Reihen von Latten auf und legt sie auf das Förderband. Auf diesem werden die Elemente mithilfe von Führungen ausgerichtet und zur Bearbeitung transportiert. Der gleiche Förderer dient auch zur Sammlung der bearbeiteten Elemente und passt automatisch seine Lade- und Aufnahmebreiten an die aktuell zugeführten Elemente an.
Sobald alle Elemente platziert sind, legt der Roboter die leeren Schwellen auf die Rollenbahn. Diese dienen als Basis für die Platzierung der verarbeiteten Latten. Der fertige Stapel der bearbeiteten Elemente gelangt automatisch von der Roboterzelle auf eine Rollenbahn, von wo aus ihn das Personal mit einem Rollenwagen abholt.
Zwischen den Förderbändern befindet sich eine Tragkonstruktion, auf der der Roboter Kartonteiler platziert. Zudem ist in der Zelle ein Quer-Schwerkraft-Kugelförderer installiert, der die manuelle Übergabe von Paketen von Papierteilern an den Rollenförderer im oberen Modus ermöglicht.
Die bearbeiteten Elemente können Noppen enthalten und werden auf Schwellen transportiert. Die maximale Stapelhöhe beträgt 1.500 mm, und die maximale Länge eines Werkstücks in der Bohrmaschine beträgt 2.400 mm.
Robotyzacja załadunku i rozładunku maszyn obróbczych

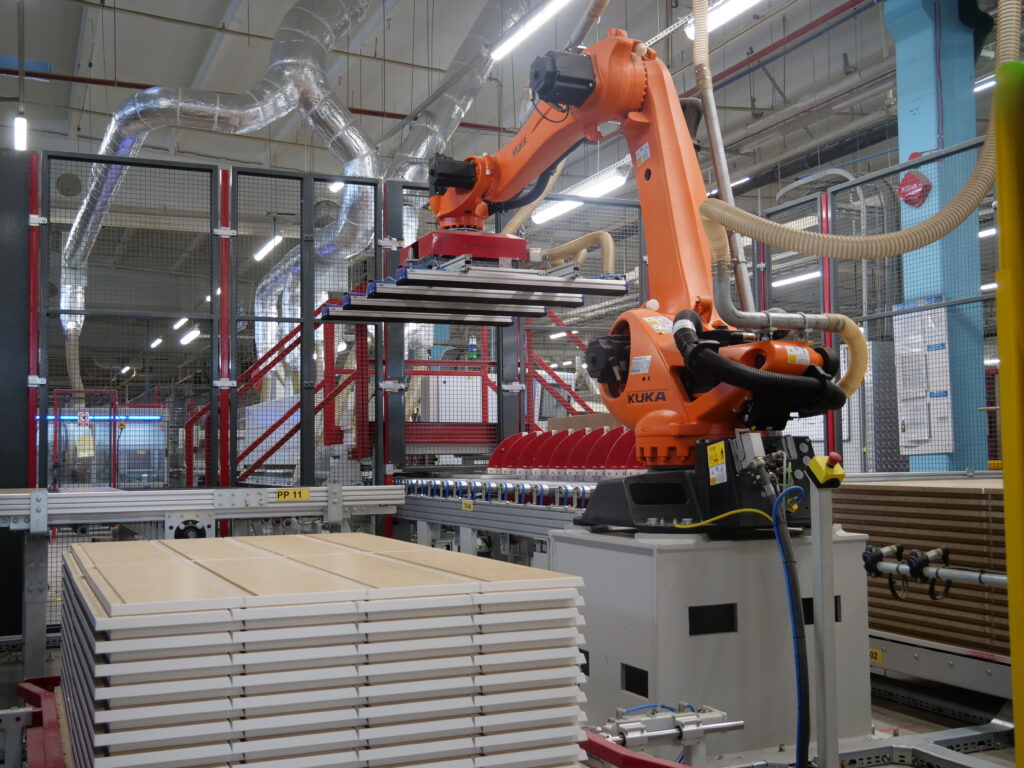
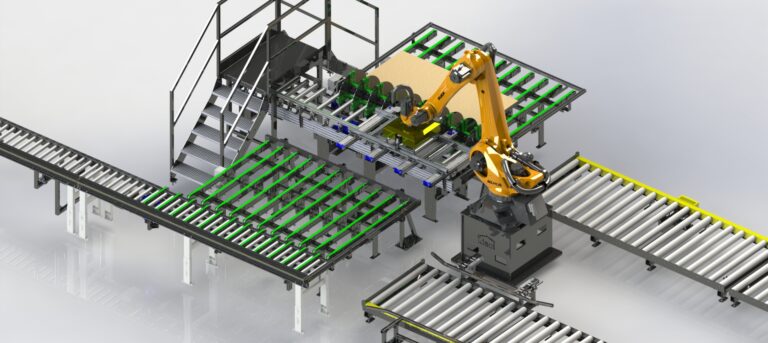
Robotyzacja procesu załadunku i rozładunku maszyn obróbczych pozwoliła na wyeliminowanie manualnego procesu wykonywania tych operacji, który skutkował niską wydajnością i małym poziomem powtarzalności. Wcześniej obsługa maszyn wymagała zaangażowania przynajmniej trzech pracowników, a robotyzacja pozwoliła na ograniczenie tej liczby do zaledwie jednej osoby.
Durch die Automatisierung der Be- und Entladung von Bearbeitungsmaschinen wurde der bisher manuelle Prozess ersetzt, der oft zu geringer Effizienz und unzureichender Genauigkeit führte. Früher waren mindestens drei Mitarbeiter für den Betrieb der Maschinen erforderlich, durch die Automatisierung konnte diese Zahl auf eine Person reduziert werden.
- Bei der Robotisierung der Bearbeitungslinie werden Elemente, die auf einer Trägerplatte angeordnet sind, mithilfe eines Roboters in eine technologische Linie mit zwei Bearbeitungsmaschinen eingespeist. Der Elementstapel wird über eine Rollenbahn in die Roboterzelle gebracht. Ein KUKA-Roboter mit Vakuumgreifer nimmt die oberste Platte vom Stapel und legt sie auf die Rollenbahn. Anschließend entnimmt er eine Lage von Elementen vom Stapel und platziert sie auf dem Querförderband. Die Elemente werden dann im Rotator gedreht und über eine weitere Rollenbahn zur technologischen Linie transportiert.
Nach der Bearbeitung werden die Elemente über eine Rollenbahn mit Hub- und Querantrieb zu den nachfolgenden Förderbändern transportiert. Zwei Produktelemente werden auf der Zwischenebene montiert. Anschließend werden die Elemente für die gesamte Lage auf den Förderbändern gesammelt und auf das Querförderband abgelegt.
Der Roboter stapelt die fertigen Lagen auf dem Förderband zu einem Elementstapel. Nachdem alle Elemente des Stapels verarbeitet wurden, nimmt der Roboter mit seinem Greifer die Trägerplatte von der Rollenbahn und legt sie als Schutzplatte auf die gestapelten Elemente. Der fertige Elementstapel wird automatisch von der Roboterzelle auf die Rollenbahn bewegt, wo er von einem automatischen Verschieber übernommen wird.
Parameter:
Abmessungen der Trägerplatte:
– Mindestmaße: 2000 × 800 × 20 mm
– Maximalmaße: 2100 × 1200 × 22 mm
Anordnung der Elemente auf der Trägerplatte:
– Elemente sind in acht Stapeln mit einem Gesamtgewicht von 2000 kg angeordnet.
Abmessungen der einzelnen Elemente:
Abmessungen der einzelnen Elemente:
– Länge: 500-1200 mm
– Breite: 200-300 mm
– Dicke: 16-23 mm
Transportgeschwindigkeit: 15-20 m/min
Produktivität: bis zu 14 Stück/Min
Załadunek i rozładunek manipulatorem w linii lakierowania wąskich krawędzi


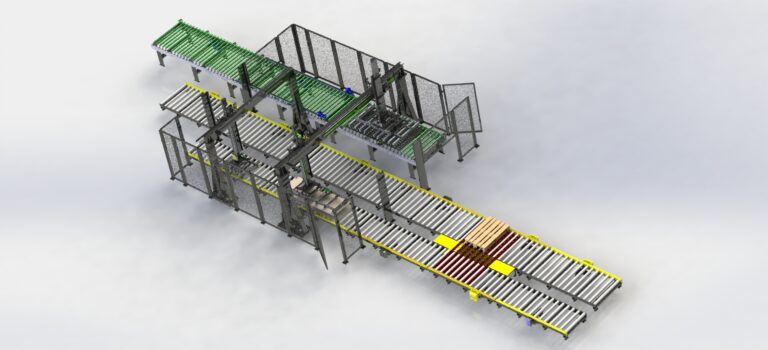
Celem naszego projektu było przede wszystkim wyeliminowanie procesu ręcznego załadunku i rozładunku linii lakierniczej, który odznaczał się niską wydajnością na poziomie 2000 szt./h, a także koniecznością zaangażowania aż sześciu osób do obsługi maszyn. Generowało to problemy z małym wypełnieniem linii i brakiem powtarzalności jakości malowania spowodowanym nierównym ułożeniem elementów na linii. Proces automatyzacji pozwolił na trzykrotny wzrost wydajności dla ułożenia elementów na pojedynczych podkładach oraz na sześciokrotny wzrost w przypadku pobrań z dwóch podkładów. Opracowana linia przeznaczona jest do lakierowania wąskich krawędzi.
Projekts waren die Eliminierung des manuellen Be- und Entladeprozesses der Lackierlinie für schmale Kanten sowie die Verbesserung der Effizienz. Vor der Automatisierung wurde die Linie nur mit einer Geschwindigkeit von 2000 Stück pro Stunde bedient, was den Einsatz von bis zu sechs Personen erforderte. Dies führte zu Problemen wie niedriger Auslastung der Linie und ungleicher Lackierqualität aufgrund ungleicher Positionierung der Teile. Durch die Automatisierung konnten wir die Effizienz des Teileladens um das Dreifache auf einzelnen Trägern und um das Sechsfache beim Laden von zwei Trägern steigern. Die entwickelte Linie ist speziell für das Lackieren von schmalen Kanten ausgelegt.
Manipulatorleistung bei der Entnahme aus einem Pad (12 Elemente pro Lage):
Manipulator-Zyklus – 7 s
Stillstandszeit des Manipulators pro Zyklus – 1 s
Anzahl der Elemente pro Zyklus – 12
Anzahl der Stapelungen pro Stunde – 514
Anzahl der Elemente pro Stunde – 6168 Stück/Stunde
Anzahl der Elemente pro Schicht – 6168 Stück/Stunde × 7,5 h = 46 260 Stück.
Da wir in der Lage sind, diese Arten von Elementen gleichzeitig auf zwei Schwellen zu entnehmen/zu platzieren, verdoppelt sich die Kapazität (12336 Elemente pro Stunde).
Anzahl der Verlegungen pro Stunde – 514
Anzahl der Elemente pro Stunde – 12336 Stück/Stunde
Anzahl der Elemente pro Schicht – 12336 Stück/Stunde × 7,5 h = 92 520 Stk.
Leistung bei der Entnahme von 3 Schwellen (14 Elemente pro Lage) – Elemente in Rahmen:
Manipulator-Zyklus – 8 s
Stillstandszeit des Manipulators in einem Zyklus – 1 s
Anzahl der Elemente pro Zyklus – 42
Anzahl der Ablagevorgänge pro Stunde – 450
Anzahl der Elemente pro Stunde – 18900 Stück/Stunde
Anzahl der Elemente pro Schicht – 18900 Stück/h × 7,5 h = 141 750 Stück.
Merkmale der eingehenden Artikel:
Elemente, die auf Paletten angeliefert werden und wie sie gestapelt sind:
- Abmessungen der Grundplatte:
1200 × 600 × 20
- Anordnung der Elemente auf der Grundplatte:
gestapelte Elemente mit einem Gesamtgewicht von 1200 kg
Abmessungen eines einzelnen Elements:
Länge – 584-1175 mm
Breite – 60-308 mm
Dicke – 14-30 mm
Funktionsweise
Die Automatisierung der Werkstückbeschickung der Lackierstraße erfolgt durch ein zweiachsiges Robotersystem, das die Werkstücke von einem Stapel auf der Rollenbahn abnimmt und auf der Rollenbahn ablegt. Bei Lattenteilen, die mit einem Spalt in die Lackierstraße eingebracht werden müssen, hat der Greifer des Robotersystems die Aufgabe, die Teile vor dem Ablegen linear um ein definiertes Maß zu verlängern, so dass die Teile in gleichen Abständen in die Straße eingebracht werden. Zusätzlich wurde ein Picking Alignment Mechanismus installiert, der dafür sorgt, dass die gegriffenen Teile bei der Entnahme richtig ausgerichtet sind. Ein Zwei-Achsen-Manipulator ist für die Entnahme der Werkstücke aus der Linie, die Entnahme von einer Rollenbahn und die Stapelung zuständig. Der Greifer des Manipulators ermöglicht auch das Stapeln der Latten im Fischgrätenmuster.
Die Positionierung der auf den Rollenbahnen transportierten Lamellen erfolgt über einstellbare, angetriebene Seitenführungen. Das transportierte Material wird außerdem durch Verriegelungen getrennt. Wir haben Siemens-Servoantriebe der Serie S210 mit einer modernen S7-1500/1500T-Steuerung eingesetzt.
Vorteile
Das von uns entwickelte System bietet jedem Kunden spezifische, messbare Vorteile, darunter: